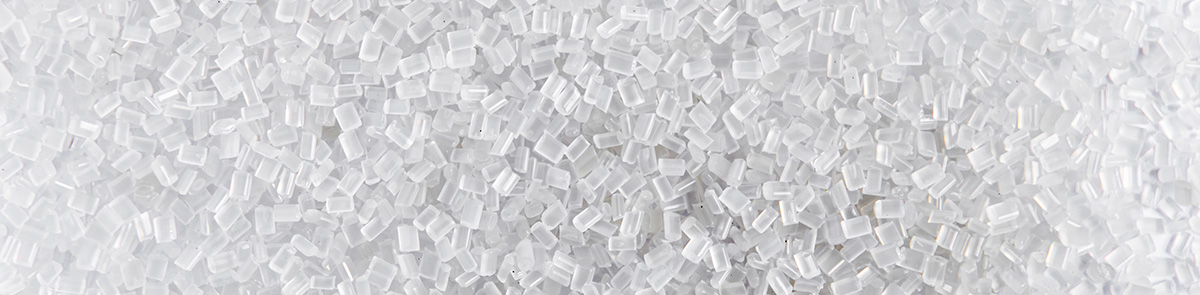
What plastics are most resistant? Are there plastics that will show scratches and wear more than others? What type of plastic is most malleable? These are all important questions you need to consider when it comes time to order or design your next part. Many of these plastics are known colloquially by abbrevations (with several starting with the letter “P”) so even a seasoned industry expert can confuse them… we’ve seen it happen!
At Buffalo Manufacturing, we want to make our custom injection molding process as simple as possible for our customers and our injection molding operators alike. Read through our list to make sure you have the appropriate product knowledge to equip yourself for your next custom injection molding part order.
8 Engineering Grade Plastics to Consider
1. Acrylonitrile butadiene styrene (ABS)
Acrylonitrile butadiene styrene, also known as ABS, is a popular choice for many in the custom injection molding process. Notability, there are two grades of ABS, ABS for injection molding and ABS for extrusion.
ABS has high impact resistance, rigidity, and temperature resistance compared to other plastic polymers. It is a highly stable plastic at both high and lower temperatures and maintains its integrity under large weight loads as well.
2. Polycarbonates (PC)
Polycarbonates (PC) is a commonly used polymer due to its durability, high level of impact resistance, and extreme temperature resistance. However, polycarbonates have low scratch resistance and many PC products require additional hard coating application to make up for this limitation.
Polycarbonates are malleable and can withstand several polymer deformations without the risk of cracking or bending. It can be molded and processed at room temperature and in some cases, does not require any heating.
Polycarbonates are excellent transmitters of visible light, commonly being used more effectively than glass in eyewear lenses and external automotive components. They are also a popular choice for prototyping parts where transparent or electrically non-conductive parts are required.
Polycarbonates are malleable and can withstand several polymer deformations without the risk of cracking or bending. It can be molded and processed at room temperature and in some cases, does not require any heating.
3. Polyamides (PA)
Polyamides (PA), most commonly known as “nylon”, are utilized for their high resistance to erosion from chemicals and abrasions, low friction surface, and their ability to be melted down and reused.
It is most commonly used in the production of fabrics and fibers, food packaging films, and in custom shape part production. Polyamides are diverse and can be mixed with a variety of different materials to achieve specific and customized product variations.
4. Polysulphone (PSU)
Polysulphone (PSU) polymers are rigid, strong, transparent, and are highly durable. It has a high compact resistance rating and is labeled as a “high-performance plastic”, commonly being used in injection molding, extrusion, and hot forming.
PSU is highly resistant to chemicals, acids, and bases on the pH scale from 2 to 13, allowing polysulphone-based parts and products to be cleaned with bleaches. However, it is soluble in dichloromethane and methyl pyrrolidone.
5. Polyetheretherketone (PEEK)
Polyetheretherketone, also known as PEEK, is highly resistant to thermal degradation and biodegradation, has low heat conductivity, and is soluble in concentrated sulfuric acid.
PEEK is a popular choice for part manufacturing in the aerospace, medical, automotive, and chemical industries because it is compatible with ultra-high vacuum applications.
6. ULTEM Polyetherimide (PEI)
ULTEM Polyetherimide (PEI) plastics have high heat, solvent, flame resistance, and low smoke generation, and are most commonly used in the production of chemical and medical instruments. PEI plastics are also known to have high strength and rigidity.
7. Polytetrafluoroethylene (PTFE)
Polytetrafluoroethylene is also known as PTFE, or more simply, “teflon”. PTFE has high strength, toughness, and self-lubrication at extremely low temperatures.
PTFE plastics are frequently used in the pharmaceutical and chemical processing industries due to its slipperiness. PTFE is also widely used as a repellent to prevent bugs, insects, and small animals from climbing on an area coated with PTFE.
8. Polyoxymethylene (POM)
Polyoxymethylene is known by many names, but is most commonly referred to as POM or “Delrin”. POM is known for its high rigidity and hardness levels, low friction, and high stability and strength making it an excellent choice for precision part products in the engineering, automotive, and electronics industries.
It is also important to note that although POM is naturally white in color, it can be manufactured into a large variety of colors, making it suitable for custom part products.
Choosing the Right Plastic for Your Part
There are several variables at play when it comes time to choose a particular plastic for your custom part. Buffalo Manufacturing offers you several different options to choose from to meet the exact specifications you need. Contact us today to get your plastic grade questions answered!